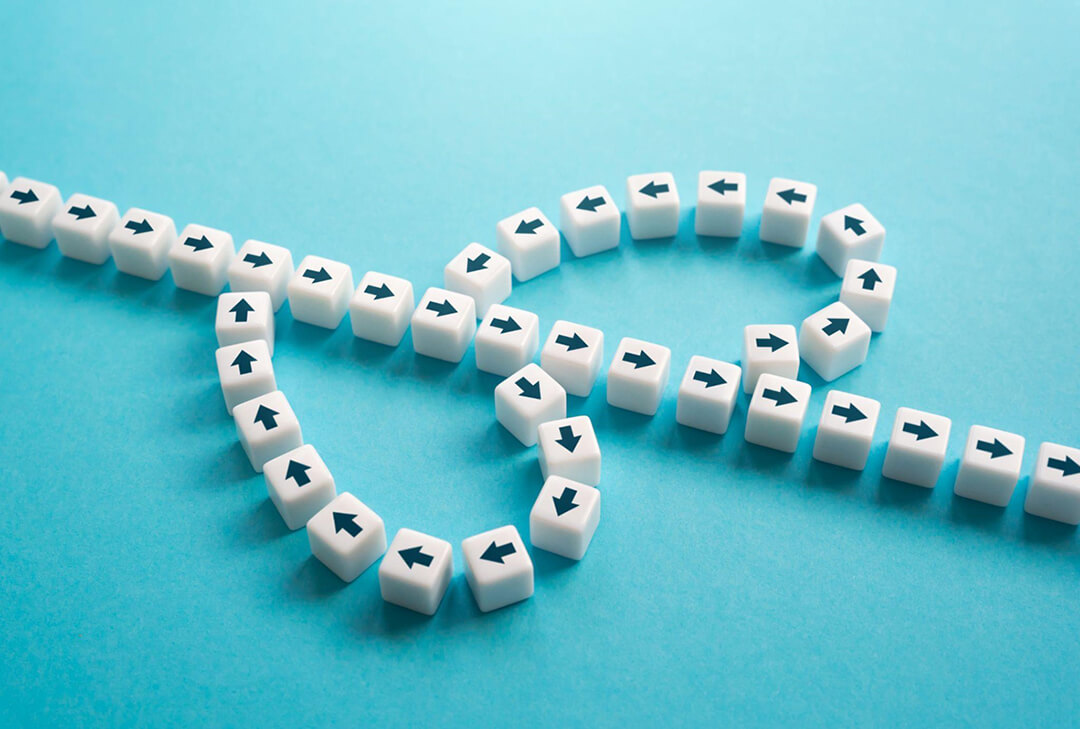
In the pharmaceutical and biotechnology industry, the key to sustainable quality is good product, process, and method development, combined with well-trained and educated personnel using well-defined systems to provide consistent results. However, as with all systems, there are occasional faults that occur. In our industry, we define these faults as “deviations.”
Deviation investigations are fundamental tools for properly identifying the root cause of these faults and creating a plan for corrective and preventive actions to bring the system back to sustainable control. But in many companies, the number of deviations is excessive and the time to complete the investigations exceeds reasonable standards. What, then, are the keys to ensure that the people assigned to investigate these deviations can do their jobs effectively, find the root cause, and propose the changes that will eliminate these faults and ensure they do not recur?
1. Analytical Mindset
The first key to being an effective investigator is the ability and desire to solve puzzles. Every deviation is like a mystery, with many factors which may be the root cause. Some of these factors, though, might be false leads which, if not properly evaluated, could result in an incorrect conclusion and a repeat of the deviation. Evaluating the capability and interest of an individual to engage in this type of exercise is the responsibility of management. Often companies make the mistake of thinking that anyone can learn the skill and perform effectively. There certainly are skills to be learned, but without this inherent interest and capability, the individual will never achieve a satisfactory level of performance.
2. Process Understanding
It is surprising how many companies assign personnel to investigate deviations who have minimal or no technical expertise in the process or product issue being evaluated. Companies would never assign someone to operate a complex process without training the individual and evaluating their competence. But often trying to unravel a root cause for a complex process is left to individuals who have never had anything but a limited overview or familiarity with the area under investigation. Taking the time to educate the investigator in the nuances of the process, product, or method will pay dividends in the speed and effectiveness of the deviation investigation.
3. Technical Writing Skill
While technical writing skill is often quoted as an important skill for deviation investigators, this is really a misnomer. The true skill required is not writing a complex technical document, but the ability to distill what is often a complex and multifaceted issue down into a clear and concise story. A critical component of every investigation is the summary report that will serve to allow company personnel and external regulators to understand the problem, the solution, and how to effectively and permanently correct the deviation. In today’s world of texts, emails, and cell phones, the ability to write clearly and concisely is a skill not necessarily well-developed in people joining our industry. But this is a skill that can be learned and should be a critical part of the training and education of personnel assigned to be investigators.
4. Knowledge of Problem Solving/Risk Evaluation Tools
There are many paths and tools available to get to the root cause of a deviation and evaluate its risk to the product or process. Pareto Charts, Fishbone Diagrams, the 5 Whys, Failure Mode and Effects Analysis (FMEA), and Risk Matrices, among many others, are all tools that can be used depending on the nature of the investigation. The selection of the wrong tool or the ineffective use of the correct one may result in a failure to find the true root cause and result in repeated instances of the same deviation. Training and education on how to choose and use the right tool must be an integral part of training for each investigator.
5. Time
Regardless of skill level, if an investigator is not given sufficient time to conduct their analysis, evaluate the risks, and draft their report, the quality and effectiveness of the investigation will be compromised. With some experience, well-trained investigators can estimate the time required to conduct and complete an investigation. When staffing for and assigning investigations, management must understand that ineffective investigations resulting in repeat deviations are far more costly than having sufficient resources available to conduct proper and thorough investigations that result in timely corrective and preventive actions. It is management’s responsibility to listen to their investigators’ estimates regarding the time required and the resources needed to do a proper evaluation.
6. Management Support for Objective Analysis
As with solving any mystery, an investigator must start their assessment without preconceived opinions or pressures. In our industry, where we are dealing with supply and cost pressures, it is a constant concern that investigators feel the weight of their efforts impacting the disposition of product. This pressure may wrongly influence investigators to construct an outcome that does not negatively impact product decisions. It is management’s responsibility to provide the leadership and organizational structure that separates the investigator from this influence. How this can be achieved is unique for every organization but, in many cases, companies can have investigators as part of an independent group, similar to internal auditors, and leave the final decisions regarding product impact as a separate activity conducted by the quality group utilizing the investigators’ findings.
Conclusion
The ability of investigators to conduct effective, objective assessments of deviations is a critical element of every company’s ability to sustainably produce safe and effective high-quality products. Selecting and training investigators who have the skills and environment to conduct well-structured and thorough analyses is the most cost-effective approach to dealing with deviations encountered during product development and manufacture.
____________________________________________________________________________
QxP Vice President Mike Levitt started his more than 30-year career in pharma leadership as Director of Production Operations at Eli Lilly and Company back in 1989.
Check out Mike’s other recent blogs: “Is it Time to Outsource Internal Auditing?” and “Pharmaceutical Quality is NOT a Spectator Sport.”