Cost Of Quality: Worth Every Cent In Bio/Pharmaceutical Manufacturing
By Crystal Mersh, CEO, Quality Executive Partners, Inc.
During my career as an executive in pharmaceutical manufacturing quality assurance, I have heard the term “cost of quality,” or “COQ” for short, over and over when advocating for budget and resources. In many cases, management has viewed budget items for improving systems, equipment, employee education, and qualifying secondary suppliers and their materials, as “nice to haves” instead of necessities. As a result, these quality system areas were not invested in as much as is necessary to ensure optimal bottom-line results.
Decisions not to invest adequately in these and other important quality areas often do not take into consideration the realities of the risk and likelihood of failure, which lead to a higher cost of poor quality (COPQ). In effect, these decisions allow for providing poor quality products and services and increasing the risk of financial loss and reputational damage. The COPQ must be built into the equation to determine COQ, and when it is, you will see that the COPQ is too high for any pharmaceutical manufacturer to endure.
The COQ is the sum of all parts of good quality AND poor quality together. The true COQ refers to your company’s acceptance and promotion of the good and the poor combined. It allows a company to decide where to add resources to mitigate failures. Most people think that the cost of quality is just an excuse for higher costs, but that is not true. The COQ is equal to prevention costs (PC) plus appraisal costs (AC) on the good side, plus the internal and external failure costs (IFC and EFC, respectively) on the poor side. Most of us have seen the equation expressed as:
COQ = PC+AC + IFC +EFC
You can see that the COQ incorporates all costs associated with maintaining acceptable quality levels. Let’s look a little deeper into these four aspects of the COQ.
Prevention Costs (PC)
Prevention costs (PC) are those that help the company minimize quality issues from arising in the first place. These costs are incurred to ensure that products are produced to meet the required quality standards. PCs include quality planning and quality system development; establishing process controls and validated processes; calibration and maintenance programs for equipment, facilities, and utilities; validated test methods with appropriate standards; continuous improvement measures including trend analysis for process and product controls; and robust training/education of the workforce. Overall, everything that leads to the basis of a solid quality system that assures defect-free output after each operation through the last step is what we are talking about here.
Appraisal Costs (AC)
Appraisal costs (AC) are associated with the measuring and monitoring of all manufacturing and testing activities related to the product manufactured. These include verification and validation of raw material testing and final product testing according to predetermined specifications with appropriate compendial standards. Internal auditing is one of the tools in the AC toolbox that provides the company with an internal look at the health of the quality system and enables the company to make changes needed to improve practices and processes. Applying rigorous and critical eyes during internal audits – whether of the systems themselves or of the manufacturing process with quality assurance (QA) staff on the floor – is a proactive way to address deficiencies before a regulatory body comes in and does that very thing. Other ACs include validation and periodic maintenance and operational checks of equipment and utilities; a supplier quality management program that mitigates supply chain risks and creates built in redundancies for higher risk items and materials; and inspection and testing of incoming materials and components for vendor-supplied material.
Now let’s look at the failure costs.
Internal Failure Costs (IFC)
Internal failure costs (IFC) are those found inside the manufacturing facility. These costs include the tangible costs after a company produces a defective or inferior product before it is shipped. IFCs include the cost of investigation or failure analysis for out-of-specification results; the cost of scrap and disposition; missing/improper documentation; delays in receiving and reviewing paperwork and planning and shipping; high employee turnover; unused facility capacity/downtime; variation in processes; and time to rework, retest, redesign, and reinspect. There are many other examples, all of which can lead to increased time to batch release and sale. These factors can lead to reductions in revenue and higher risks of competitors gaining market share, especially for those companies that are multi-generic manufacturers. Any time the prefix starts with “re”, you are losing time, efficiency, and money on the manufacturing floor.
External Failure Costs (EFC)
External failure costs (EFC) include the tangible along with the intangible costs once the product is distributed to the customer. These costs can impact your business significantly and put your business at risk reputationally and competitively. Tangible costs are those like recalls (which include the personnel hours to determine the extent of the recall) and returned goods costs. Overdue receivables can result because you are in a state of investigation into failures including materials, components, etc. Lack of future sales can be part of the tangible, as are the costs of customer complaints, customer returns, and excess inventory. The intangible costs can be incalculable and can cause you the most harm. These include reputation harm, regulatory action taken, competitive disadvantage, damage of goodwill, and not being able to meet the goal of serving patients’ needs.
Pharmaceutical manufacturers with a history or reputation of poor quality are apt to be inspected more often by regulatory agencies. They run the risk of regulatory actions that could impede the sale of their medicines. In the mid- to long run, these companies will incur higher failure costs and reputational harm. In comparison, pharmaceutical manufacturers that invest in good quality measures will incur a lower total COQ and keep their promise of delivering quality medicines to patients and serving as the backbone of a healthy supply chain.
As leaders in the pharmaceutical manufacturing industry, when thinking of the cost of quality, make sure your company thinks of the entire equation: COQ = PC+AC +IFC +EFC. I’ll bet you will find that the cost of quality is worth every penny and the COPQ is too much for your company to endure, just as many of our clients have discovered over the past decade.
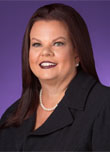
About The Author:
Crystal Mersh is the founder and CEO of Quality Executive Partners, Inc. (QxP). Her career in pharma quality has spanned three decades and across large companies. Prior to founding QxP in 2012, she held leadership roles in quality at Mylan, Novartis, Watson Pharmaceuticals, and Sanofi.