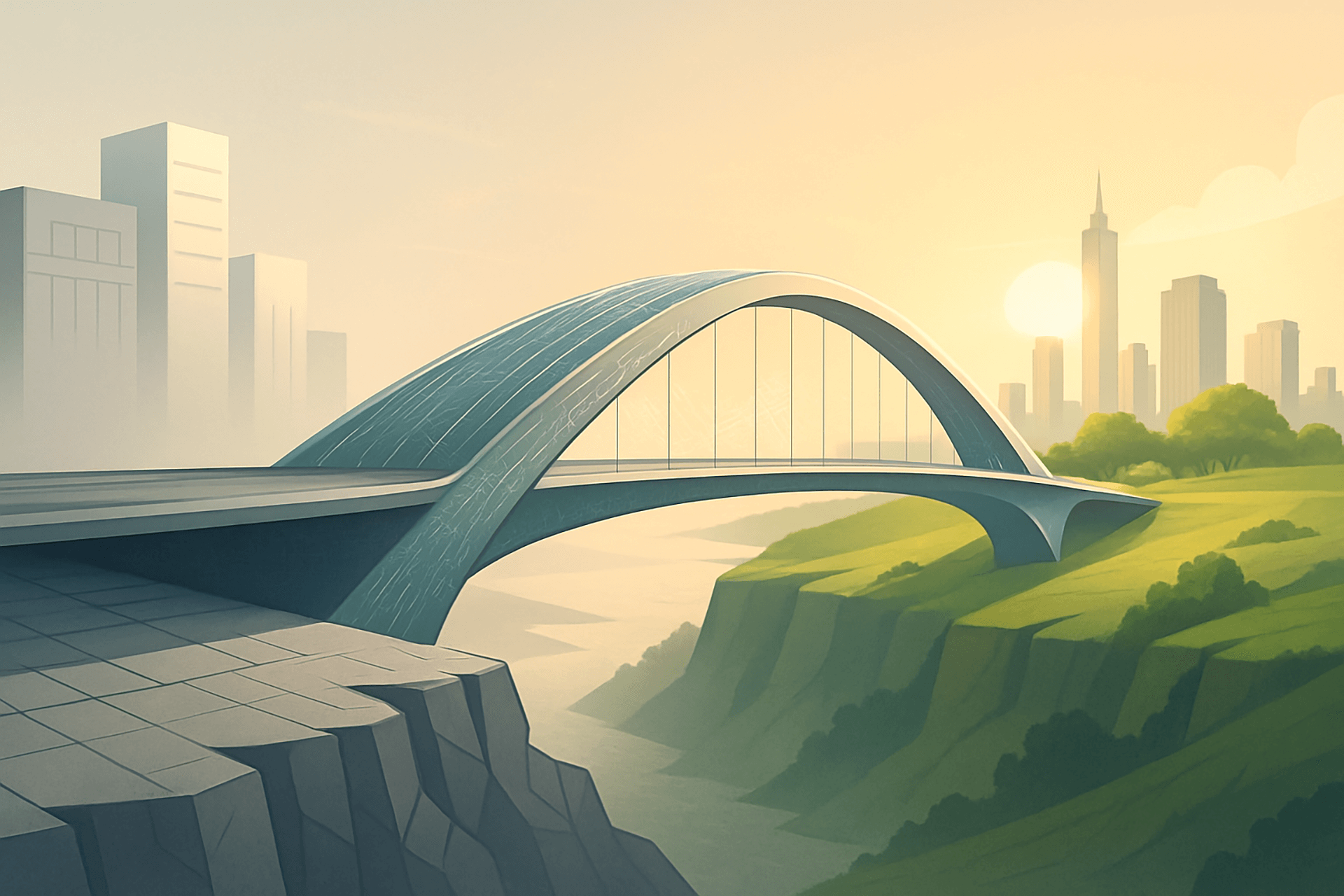
In the pharmaceutical industry, quality metrics are often viewed through a regulatory lens — and for good reason. The FDA’s Quality Metrics Initiative and global standards like ICH Q10 have elevated the role of performance indicators in demonstrating a state of control. But beyond compliance, these metrics provide critical business intelligence — identifying process gaps, reducing cost, and improving patient outcomes.
Tracking quality metrics isn’t just about surviving audits; it’s about building a resilient, trustworthy, and competitive operation.
Key Quality Metrics That Matter— For Compliance and Business
1. Right First Time (RFT)
- What it Measures: % of batches produced without deviations, rework, or rejection.
- Why it Matters: High RFT reduces cost, waste, and regulatory risk.
Real-World Example (Manufacturing):
A global generics manufacturer noticed that its RFT rate had dipped below 85% for a particular oral solid dosage line. Root cause analysis revealed inconsistent granulation parameters across shifts. By standardizing procedures and retraining operators, RFT improved to 96%—resulting in a $1.2 million annual saving in reduced rework and batch delays.
2. Deviation Rate
- What it Measures: Number of deviations per 1,000 batches or per manufacturing site.
- Why it Matters: High deviation rates can signal deeper systemic or process control issues.
Real-World Example (Quality Assurance):
A biologics company saw a spike in temperature excursion deviations during transport. Investigation revealed poor integration between quality and logistics vendors. They introduced a digital temperature monitoring solution and vendor requalification, reducing transport deviations by 75% and avoiding potential product write-offs.
3. CAPA Effectiveness
- What it Measures: How often corrective actions resolve root causes without recurrence.
- Why it Matters: Ineffective CAPAs are a red flag during inspections.
Real-World Example (Quality Systems):
Following an FDA 483, a sterile injectables plant launched a CAPA related to inadequate visual inspection training. However, complaints about particulate matter continued. A second root cause analysis revealed the issue was not training, but defective lighting in the inspection area. The CAPA was revised, and the FDA later acknowledged the improved inspection program in a follow-up visit.
4. Batch Failure Rate
- What it Measures: Number of failed lots per total lots produced.
- Why it Matters: High failure rates affect market supply and regulatory standing.
Real-World Example (Manufacturing):
An API manufacturer with a 4% batch failure rate traced most failures to cleaning validation residues. With improved cleaning protocols and equipment upgrades, the failure rate dropped to below 1%, preserving $5 million in annual revenue and avoiding a potential import alert.
5. Customer Complaints
- What it Measures: Volume and severity of product complaints.
- Why it Matters: Indicates real-world product performance and patient safety.
Real-World Example (Commercial Quality):
A branded pharma company experienced a 40% rise in complaints for a transdermal patch peeling off prematurely. Investigation linked the issue to humidity during secondary packaging at a contract manufacturing site. After implementing stricter environmental controls and packaging redesign, complaints fell to baseline levels and market share recovered within two quarters.
6. Product Recall Frequency
- What it Measures: Number of recalls, their classification, and root causes.
- Why it Matters: Recalls hurt revenue, brand equity, and regulatory relationships.
Real-World Example (Global Operations):
A company faced two consecutive Class II recalls due to mislabeling of strength on injectable vials. Implementing a vision-based automated label verification system at all packaging lines virtually eliminated labeling errors, contributing to a 3-year recall-free streak and improved FDA inspection outcomes.
7. On-Time Closure of Quality Events
- What it Measures: % of investigations, deviations, and CAPAs closed within defined timelines.
- Why it Matters: Timely closure reflects good governance and reduces compliance risk.
Real-World Example (QA/QC):
A multinational site struggled to close CAPAs on time (only 65% closed within 30 days). This was flagged during an EMA inspection. After implementing a risk-based prioritization system and integrated QMS workflow, on-time closure improved to 92% within six months, reducing regulatory risk and boosting team accountability.
8. Supplier Quality Metrics
- What it Measures: % of on-time deliveries, deviation rates, and audit performance.
- Why it Matters: Poor supplier performance disrupts production and creates compliance gaps.
Real-World Example (Supply Chain):
A sterile product manufacturer experienced inconsistent raw material quality from a key excipient supplier, leading to frequent OOS results. They introduced a supplier scorecard system, conducted a joint audit, and worked collaboratively to improve the supplier’s in-process testing controls. The issue was resolved, and the supplier was re-classified as preferred—restoring supply stability and minimizing testing failures.
Why These Metrics Are Good for Business
Quality metrics tell a compelling story—not just to regulators, but to executives, shareholders, and patients. Companies that leverage them can:
- Prevent costly disruptions from recalls, rejections, or inspections.
- Benchmark performance across sites, CMOs, and suppliers.
- Drive digital transformation by integrating QMS, MES, and ERP systems.
- Foster continuous improvement culture tied to tangible KPIs.
- Enhance market agility by freeing up resources wasted on rework and firefighting.
Final Thoughts: Metrics with Meaning
In a world of increasing regulatory scrutiny and competitive pressure, pharmaceutical companies can no longer afford to treat quality metrics as an afterthought. Real-world outcomes—whether in manufacturing, quality, or the supply chain—prove that metrics not only ensure compliance, they unlock operational excellence.
When used intelligently, these indicators become more than numbers; they become levers for change, trust, and growth.
Let us show you the Value of Quality and what this means to your business.
QxP Vice President Christine Feaster is a 20+ year veteran in pharma quality assurance. Prior to joining QxP, Christine was a vice president of U.S. Pharmacopeia.